Supply Chain Planning
Imagine standing at the helm of a vast network where every decision ripples across continents, affecting thousands of products and countless consumers. That’s supply chain planning in action. You’re constantly balancing customer demands against inventory costs, manufacturing capabilities, and supplier limitations. It’s a complex dance that requires precision, foresight, and adaptability. In today’s volatile market, effective supply chain planning isn’t just a competitive advantage—it’s the difference between thriving and merely surviving. The question is: Are you orchestrating this symphony or just reacting to its chaos?
Supply Chain Planning Definition
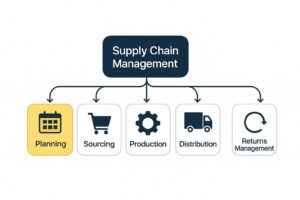
Demand Forecasting
The cornerstone of efficient supply chain planning, demand forecasting predicts future product needs based on historical data, market trends, and other influential factors. Your forecasting accuracy depends heavily on data quality and the methods you choose.
You’ll need to select appropriate techniques based on your specific situation. Qualitative methods work when historical data is limited, while time series analysis identifies patterns in existing sales data. Managing demand variability requires combining approaches—statistical models with causal inferences often yield the most thorough results. AI-powered solutions are increasingly being adopted by forward-thinking organizations to handle complex data sets and improve prediction accuracy. The DoD extensively relies on quantitative models that incorporate historical demand alongside future program data for more reliable forecasts.
When implemented properly, demand planning will guide your pricing strategies, optimize inventory levels, inform labor planning, and streamline procurement. Developing digital twins can significantly enhance your ability to test multiple scenarios without disrupting actual operations. Effective forecasting helps balance delivery times against customer wait expectations, especially when supply chain lead times exceed customer order expectations. The COVID-19 pandemic has demonstrated the crucial importance of rapid adaptation in forecasting methodologies. However, you’ll face challenges like market volatility and technology integration. The strength of your supply chain ultimately hinges on how well you anticipate customer demand.
Inventory Management
Building on your demand forecasting foundation, inventory management forms the operational backbone of your supply chain planning process. It’s the systematic approach that determines what to order, how much to order, and tracks stock throughout its journey.
Effective inventory optimization strategies balance carrying costs with service expectations, preventing both costly overstocking and reputation-damaging stockouts. You’ll need to implement stock tracking technologies that provide real-time visibility across your supply chain, enhancing your decision-making capabilities. Implementing structured methods like ABC analysis allows businesses to classify inventory based on importance and consumption value. The proper categorization of raw materials, parts and components, work in progress, and finished goods enables precise tracking throughout the production cycle. Maintaining optimal inventory levels is essential for enhancing customer loyalty through consistent order fulfillment and positive experiences.
When properly executed, inventory management reduces working capital requirements while ensuring product availability when customers need it. It connects all stages of your supply chain—from procurement to sale—creating a centralized hub that promotes resilience during any supply chain disruptions. With the integration of blockchain technology, tracking materials and maintaining transparency becomes significantly more efficient. Regular audits and cycle counts will maintain accuracy, allowing you to meet customer commitments consistently while minimizing waste.
Response and Supply Planning
Moving beyond inventory tracking, response and supply planning form the proactive element of your supply chain strategy, enabling you to anticipate and react to market fluctuations with precision. This strategic process aligns production capabilities with forecasted demand while building in supply chain agility.
Effective planning considers your capacity constraints, supplier reliability, and potential disruptions—from weather events to geopolitical instability. By utilizing advanced analytics and real-time data, you’ll develop response strategies that balance cost optimization with service levels.
The benefits are substantial: reduced costs, minimized disruptions, enhanced profitability, and improved customer satisfaction. Your planning technology stack should include scenario modeling tools that enable cross-functional collaboration and provide end-to-end visibility, which are components for adapting quickly when circumstances change.
Sales and Operations Planning (S&OP)
At the heart of effective supply chain management, Sales and Operations Planning (S&OP) serves as an integrated business process that aligns your demand, supply, and financial planning within a unified framework. This essential process balances your business functions to achieve organizational synchronization while supporting executive decision-making. The process typically follows a monthly cycle with weekly check-ins to ensure all departments remain aligned toward common objectives.
Implementing S&OP offers significant benefits, including optimized resource utilization, improved lifecycle management, and consistent achievement of KPIs. The process starts with global aggregate demand as the foundation for all subsequent planning activities. S&OP evolved from aggregated production planning in the 1950s before being formalized by Richard Ling in the 1980s. Effective S&OP requires cross-functional collaboration between sales, operations, marketing, procurement, manufacturing, transportation, and finance teams to create a unified production plan. However, you’ll face S&OP challenges like ensuring horizontal alignment between departments and vertical alignment between strategy and operations.
Your S&OP metrics should track the effectiveness of reconciling demand with production capabilities while managing financial requirements. Companies implementing S&OP can expect to eliminate departmental silos and align crucial data points for increased organizational efficiency. Modern S&OP tools facilitate data gathering, demand forecasting, and production planning across your agreed rolling horizon. Whether you’re considering traditional S&OP or evolving to Integrated Business Planning, the focus remains on future actions rather than past performance.
Production planning
While many components influence supply chain success, production planning forms the essential blueprint that guides your entire manufacturing process. It maps out all required resources, steps, and timelines to transform materials into finished products that meet customer demand.
Effective production planning optimizes both customer-facing and internal processes by determining what to produce, when to produce it, and how much to produce. You’ll need to forecast demand, evaluate resource allocation options, and select the most cost-effective approach to maximize production efficiency. Establishing a structured process with flexible rules ensures production planning effectiveness across different business environments. Modern production planning has evolved to incorporate advanced technological systems that enhance communication and monitoring capabilities. Implementing various production planning types like batch, flow, or job-based manufacturing can significantly increase operational efficiency based on your specific industry needs.
The process integrates closely with other supply chain functions, including demand forecasting, inventory management, and S&OP. By minimizing lead times and balancing capacity with demand, you’ll avoid shortages while preventing excessive inventory that ties up capital.
Demand-Driven Replenishment (DDMRP)
Demand-driven replenishment (DDMRP) represents a paradigm shift in supply chain planning that addresses the fundamental limitations of traditional forecast-based methods. By strategically positioning inventory buffers at critical decoupling points, you’re able to absorb demand variability while maintaining ideal service levels.
Unlike traditional MRP, DDMRP bases replenishment decisions on actual consumption rather than unreliable forecasts. This approach minimizes the bullwhip effect through effective buffer management, creating a more agile and responsive supply chain. Microsoft has integrated DDMRP capabilities into Dynamics 365 Supply Chain Management with no additional fees required.
You’ll find DDMRP particularly valuable when customer-required lead times fall short of cumulative supply lead times. The five-component methodology—strategic positioning, buffer profiles, dynamic adjustments, demand-driven planning, and visible execution—helps you reduce both stockouts and excess inventory while improving overall flow and responsiveness to market fluctuations. The implementation of DDMRP can significantly enhance on-time delivery performance across your organization. DDMRP combines elements from various methodologies including MRP, DRP, Lean, Theory of Constraints, and Six Sigma to deliver a comprehensive planning approach across different manufacturing environments. With DDMRP, your organization can achieve enhanced operational responsiveness by eliminating the traditional dependence on complex spreadsheets for resource planning.
Supply Chain Monitoring
Supply chain monitoring forms the nervous system of your planning infrastructure, constantly tracking, analyzing, and reporting on production and distribution processes across your network. It enables real-time visibility into inventory levels, lead times, and supplier performance to support proactive decision-making.
With effective monitoring, you’ll detect potential disruptions before they impact operations, strengthening your risk mitigation capabilities. Modern monitoring solutions provide periodic data insights similar to Lifecycle dashboards that refresh weekly to ensure accurate supply chain health assessment. IoT sensors, AI-powered analytics, and cloud-based platforms provide the technological foundation for thorough oversight. These tools help you track critical performance metrics, including order fulfillment rates, inventory turnover, and supplier compliance. The monitoring phase is crucial for continuous flow models that depend on stable demand forecasting in mature industries. Effective monitoring also aligns with the SCOR Model, which helps companies make strategic decisions and improve processes.
The benefits extend beyond operational efficiency—you’ll reduce costs, enhance customer satisfaction, and maintain regulatory compliance through thorough audit trails and documentation. Implementing comprehensive monitoring solutions also supports scenario planning by providing the real-time data needed to prepare for multiple potential futures. Communication between stakeholders remains essential for ensuring that monitoring insights lead to actionable improvements across the supply chain components and players. This continuous feedback loop drives ongoing optimization throughout your supply chain.
Network Design
The foundation of effective supply chain planning rests on network design – the strategic blueprint that maps how your products flow from suppliers to customers. This three-tiered approach (strategic, tactical, and operational) creates a working model that balances service levels with manufacturing, inventory, and transportation costs.
Your network design should incorporate facility layout decisions based on proximity to suppliers and markets, while optimizing transportation routes to minimize expenses. Through network optimization, you’ll connect multiple supply chains using mathematical frameworks that represent all components from storage systems to inventory management strategies. Evaluating new technologies before implementation is essential to understand their impact on your supply chain network performance. Data-driven decision making enables more accurate modeling and helps identify the most cost-effective solutions for your network configuration. Approximately 80% of costs are determined during this critical design phase, making it essential to get the network structure right from the beginning.
When designing your network, consider what-if scenarios to assess the impacts of demand shifts or cost fluctuations. Running various simulations helps businesses develop contingency plans that enhance overall supply chain resilience against potential disruptions. Effective information systems enable visibility across your entire supply chain, supporting both planning and execution decisions. Determining the ideal placement of distribution centers is crucial for maximizing speed and flexibility throughout your logistics network.
Supply Chain Planning Process Flow
Effective supply chain planning follows a sequential process that begins with anticipating customer needs. You’ll start by analyzing historical sales data, market trends, and external factors to forecast future demand, forming the foundation for all subsequent activities. This forecasting drives supply chain collaboration across departments.
Next, your S&OP process serves as the organizational heartbeat, balancing volume requirements with business objectives and creating cross-functional alignment. With demand clarity established, strategic sourcing follows as you identify suppliers, negotiate contracts, and determine inventory levels.
Production planning then converts these inputs into manufacturing schedules, considering capacity constraints and resource availability. KPIs and metrics provide essential data-driven insights for evaluating efficiency and identifying optimization opportunities throughout your processes. Risk management strategies should be implemented to identify potential disruptions and develop contingency plans accordingly. Throughout this process, it’s essential to involve various stakeholders including sales, finance, marketing, operations, and product management in regular meetings to keep teams updated on planning progress. The implementation of inventory management systems helps monitor stock levels and prevents shortages or excess inventory. Finally, your inventory and logistics management optimizes transportation routes and product flow, ensuring the right goods reach customers at the right time while maintaining appropriate stock levels.
Supply Chain Planning Technology and Solutions
Modern supply chain planning solutions now integrate seamlessly with ERP systems while leveraging algorithmic approaches to optimize decision-making across your network. You’ll find that big data capabilities enable these platforms to process vast amounts of information from multiple sources, creating a more responsive and accurate planning environment. The most advanced solutions incorporate artificial intelligence to identify patterns, predict disruptions, and automatically suggest corrective actions that human planners might overlook. Leading providers like Oracle and SAP offer comprehensive platforms that support demand forecasting through historical data integration with current market trends. Organizations can improve business performance through machine learning simulations that generate accurate forecasts while tracking errors in real-time. Advanced inventory planning technologies can deliver 99+% availability while simultaneously reducing overall stock levels. Kinaxis has been recognized as a Leader in the Gartner Magic Quadrant for Supply Chain Planning Solutions for eleven consecutive years. These platforms establish a single version of truth for planning data and decisions across various execution environments.
Supply Chain Planning and ERP systems
Integrated planning with ERP systems represents a cornerstone of operational excellence in today’s competitive marketplace. When you connect your planning processes with enterprise systems, you’ll achieve collaboration efficiency through streamlined information flows between business units. Data integration enables procurement managers to make superior purchasing decisions based on accurate supplier and demand information. Material requirements planning functionality ensures raw materials are available precisely when needed in the production process. ERP systems generate forecasts using both historical data and real-time information to optimize supply chain operations.
Your ERP implementation should focus on modules that include planning, procurement, and inventory management capabilities. With integrated systems, you’ll gain real-time visibility into inventory levels, production schedules, and delivery statuses. This visibility translates into better customer experiences through accurate delivery estimates and consistent order fulfillment. Automated procurement workflows substantially reduce manual errors while standardizing procedures across your organization. Advanced systems enable enhanced inventory management that balances supply and demand while minimizing excess stock levels. Implementing ERP solutions helps overcome siloed data challenges that traditionally create communication barriers between departments.
The unified view of your business data will ultimately enhance strategic decision-making and allow you to respond quickly to changing market conditions.
Algorithmic Supply Chain Planning
As businesses navigate increasingly complex global operations, algorithmic supply chain planning has emerged as a transformative approach to operational excellence. By leveraging predictive analytics and machine learning, you’ll gain algorithmic insights that dramatically improve forecasting accuracy while reducing stockouts and excess inventory.
Modern platforms like RELEX and Arkieva integrate real-time data analysis, allowing you to shift from monthly to continuous weekly planning cycles. These unified solutions provide end-to-end visibility, optimizing everything from demand forecasting to inventory management in a single environment.
The true power lies in continuous improvement – retrospective analysis compares actual outcomes against predictions, refining your algorithms over time. This creates a feedback-driven planning process that adapts to market shifts while consistently improving service levels and reducing working capital requirements.
Big Data in Supply Chain Planning
Big data has revolutionized supply chain planning by transforming vast amounts of information into actionable intelligence. You’ll gain enhanced visibility across operations, allowing real-time monitoring of inventory, shipments, and potential bottlenecks.
Through big data analytics, you can optimize inventory levels based on accurate demand forecasting, reducing both stockouts and excess inventory costs. Predictive modeling identifies potential disruptions before they impact your operations, enhancing resilience against external challenges.
Your customer experience improves as you leverage data for personalized fulfillment and transparent communication. Efficiency gains come through route optimization and automated logistics, while sustainability benefits emerge from data-driven green initiatives.
Artificial Intelligence Supply Chain Planning
Artificial intelligence has transformed supply chain planning into a strategic powerhouse, with 98% of companies now integrating AI solutions as of Q1 2025. Your organization can achieve remarkable results through AI optimization, including 15% reduced logistics costs and 35% lower inventory levels.
Predictive analytics capabilities now identify 80% of potential inventory risks before they occur, enabling proactive risk mitigation across your operations. The automation benefits extend beyond efficiency—you’ll gain operational insights that drive strategic alignment with broader business objectives.
Data integration across your supply chain enhances visibility and transparency, allowing your team to track performance metrics in real-time. Companies like Sanofi demonstrate the competitive advantage, avoiding €300 million in revenue risks through AI-powered inventory management and demand forecasting.
Examples of Supply Chain Planning
Co-packers serve as critical partners in supply chain planning, as demonstrated by The Clorox Company’s structured approach to managing its external manufacturing relationships. You’ll find that Clorox implements a thorough process that includes supplier qualification, capacity planning, and performance monitoring to guarantee their co-packing arrangements align with production needs and consumer demand. Their systematic approach illustrates how effective co-packer integration can streamline operations while maintaining quality control throughout the supply chain network.
Co Pack
The strategic use of co-packing represents a critical solution for companies looking to optimize their supply chain operations without investing in extensive packaging infrastructure. When integrating co-packing into your planning strategy, you’ll realize significant co-packing benefits, including reduced costs, shortened lead times, and the ability to focus on core production activities while experts handle your packaging needs.
Despite these advantages, you’ll need to navigate co-packing challenges such as finding reliable partners and ensuring quality control throughout the process. Co-packing serves multiple strategic purposes—from creating promotional bundled offerings to managing capacity constraints when your facilities reach maximum production. It’s particularly valuable when you need specialized packaging expertise but can’t justify the capital investment for in-house capabilities. Your ERP systems can effectively manage these subcontracting relationships to maintain supply chain visibility.
The Clorox Company Supply Chain Planning Process
While examining successful supply chain planning models, Clorox Company stands out with its thorough and integrated approach that you can learn from. Their end-to-end supply chain integration aligns planning, sourcing, manufacturing, and logistics under a chief product supply officer with “integrator” roles bridging business units and supply chain functions.
You’ll notice how Clorox embeds supply chain leadership within business units, providing holistic views on demand, supply, and financial trade-offs. Their systematic risk assessment methodology evaluates suppliers through third-party audits and self-assessments, categorizing them for tailored engagement.
What makes Clorox’s process effective is its consumer-centric focus—planning objectives emphasize agility and lean operations while data-driven processes integrate consumer insights into execution, creating a responsive and adaptive supply chain system.
Why Is Supply Chain Planning Such an Important Activity?
Supply chain planning stands as a cornerstone of modern business success, impacting virtually every aspect of an organization’s performance and sustainability. Through effective supply chain alignment and risk mitigation, you’ll position your company to withstand disruptions that affect 57% of businesses’ revenue and can cause up to 62% in financial losses.
The numbers speak for themselves: companies with optimized supply chains enjoy 15% lower costs, while 79% of high-performing supply chain organizations achieve above-average revenue growth. You’ll gain a competitive advantage through improved resource allocation, reduced inventory costs, and enhanced customer satisfaction. In today’s market, where 73% of supply chains face pressure to improve delivery capabilities, proper planning isn’t just beneficial—it’s essential for survival and market leadership.
Frequently Asked Questions
How Does AI Impact Modern Supply Chain Planning?
You’re leveraging AI algorithms for demand forecasting with predictive analytics. It’s transforming your supply chain through automated decision making, inventory optimization, and risk management, reducing costs while improving efficiency and responsiveness.
What Skills Are Essential for Supply Chain Planning Professionals?
Drowning in today’s business complexity? You’ll need analytical thinking to extract meaningful insights and communication skills to collaborate effectively. Technical knowledge, digital capabilities, relationship management, and adaptability are also essential for your supply chain success.
How Do Sustainability Goals Affect Supply Chain Planning?
You’ll need to integrate sustainable sourcing and carbon footprint reduction into every decision. They’ll reshape your supplier selection, transportation methods, inventory levels, and technology investments to meet regulatory and stakeholder expectations.
What Are Common Supply Chain Planning KPIS?
Keeping your finger on the pulse, you’ll need key KPIs like demand forecast accuracy, perfect order rate, inventory turnover, and cash-to-cash cycle time to drive supply chain efficiency and monitor performance.
How Often Should Supply Chain Plans Be Reviewed?
You should adjust your review frequency based on the plan level: strategic plans annually, tactical plans quarterly, and operational plans monthly. Weekly monitoring guarantees plan adaptability during market changes or supply disruptions.
Conclusion
Supply chain planning isn’t just a business process—it’s the heartbeat of your operations. You’ll find that effective planning transforms forecasting, inventory, and response strategies into competitive advantages. By embracing advanced solutions and collaborative approaches, you’re not only reducing costs but also strengthening customer loyalty. Like a conductor leading an orchestra, proper supply chain planning harmonizes all elements to create a masterpiece of operational efficiency.